Our client, a globally renowned automotive manufacturer with decades of industry leadership, faced increasing pressures to meet rising consumer demands for innovative vehicles while maintaining the highest standards of quality. Operating on a massive scale, the client’s production facilities were spread across multiple locations, making efficient and coordinated manufacturing a complex challenge. As a forward-thinking company, they recognized the need to modernize their production processes to stay competitive in a rapidly evolving automotive landscape.
The Chalange
Despite their esteemed position in the automotive sector, our client encountered several critical challenges:
Legacy Systems Strain: Aging data capture systems struggled to handle the growing complexities of modern automotive production, resulting in operational inefficiencies and delays.
Global Operations Coordination: Coordinating production activities across multiple facilities proved challenging due to the lack of real-time insights, hindering their ability to respond swiftly to changes and optimize workflows.
Stringent Quality Standards: The client’s commitment to delivering top-notch quality faced hurdles, as real-time monitoring and quick identification of quality issues were lacking.
Our Solution:
In response to these challenges, SRKS implemented a tailored Real-Time Data Capture and Monitoring System, designed to address the specific needs of our client:
Modernized Data Infrastructure: Upgraded the client’s data capture infrastructure to handle the intricacies of contemporary automotive manufacturing, ensuring real-time data availability.
Global Connectivity: Implemented IoT devices and a centralized data hub to connect manufacturing equipment across all facilities, fostering real-time collaboration and data sharing.
Quality Assurance Overhaul: Introduced real-time quality control measures, leveraging data insights to proactively identify and rectify quality issues, ensuring compliance with the client’s stringent standards.
Predictive Maintenance Integration: Incorporated predictive analytics to anticipate equipment failures and schedule maintenance activities, reducing unplanned downtime and increasing overall equipment effectiveness.
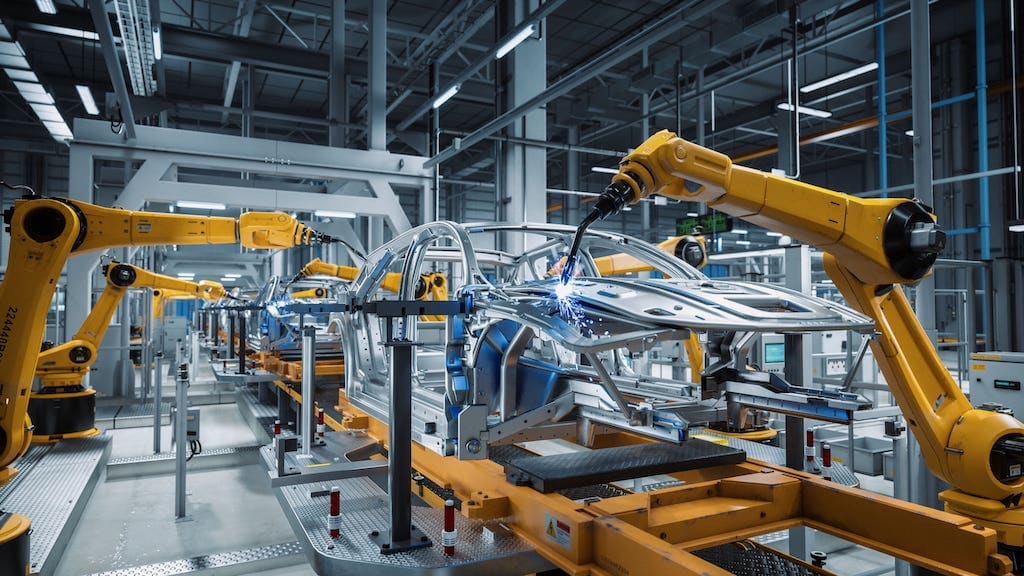
The Results
- Operational Efficiency Gains: Real-time data availability led to the identification and elimination of bottlenecks, resulting in streamlined production processes and increased operational efficiency.
- Elevated Quality Standards: Proactive quality control measures significantly reduced defects, enhancing the overall quality of the client's automotive products.
- Global Coordination Success: The centralized data hub facilitated real-time collaboration, enabling seamless coordination and synchronization of production activities across all facilities.
- Cost Reductions: Predictive maintenance and optimized resource allocation resulted in reduced downtime, translating into significant cost savings for the client.